Fuel injection - how injection works
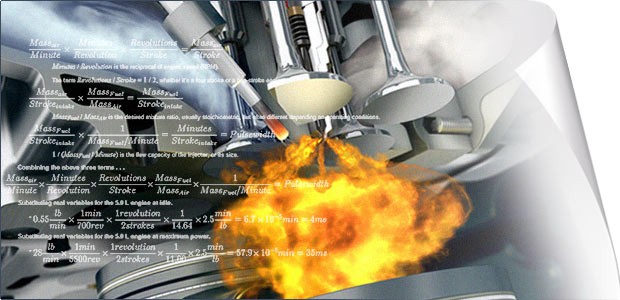
Fuel injection
Mixing fuel and air in today's way
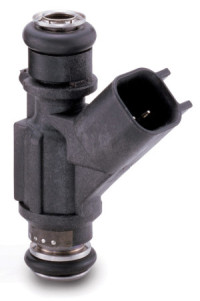
Multec 3.5 Gasoline Injector (Delphi Corporation)
Today's fuel injection systems are proof that electronics can sometimes be attractive (even to fans of traditional, classic, or old vehicles :-)).
But, let's be clear, fuel injection existed before all electronics. Back then, it was called, you guessed it, "mechanical fuel injection" and it made the big and expensive sedans of the XNUMXs real engineering gems. Admittedly, fuel injection, and even direct injection, was conceived and applied in practice far before the XNUMXs, but we will talk more about that at the end of this article.
Basically fuel injection under (high) pressure is actually a very simple thing. The intake system now consists only of a butterfly and a suction pipe and / or a intake manifold into which a fuel injection injector is "inserted". This injector is, in fact, a valve that leaks fuel under pressure into a stream of air inside the intake manifold. The injector can be placed on the suction pipe just in front of the cylinder inlet (in front of the suction valve) or in front of the butterfly (or both).
Unlike a sprayer that discharges fuel through an adjustable nozzle into the intake manifold diffuser, the injection system is much simpler, because a mixture of fuel and air is created just before suction valve. This simplifies the design of the suction pipe, which now only has to take care of proper airflow.
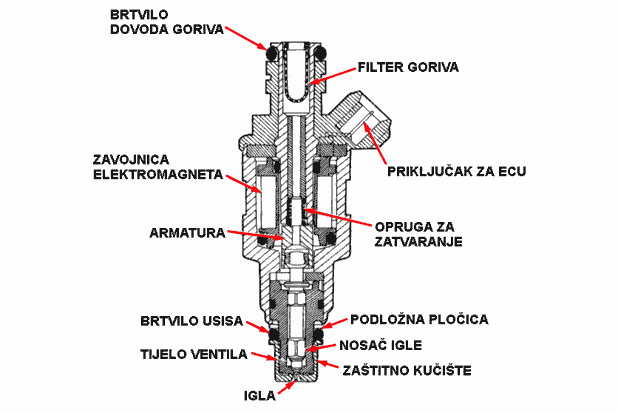
Electromagnetic syringe construction (height: 80 mm)
The mechanical injection system that was once used had a fuel rail that supplied each injector with the right amount of fuel at a given time. These injectors had a needle valve (a valve that opens and closes by moving a small rod - needle) that opened under fuel pressure and was closed by a built-in spring.
The benefits that electronics have brought us have created injection as we know it today - electronic fuel injection. The story is similar here as well, with the difference that there are no fuel distributors, and the injectors are electromagnetic, which means that their opening is controlled by electrical impulses.
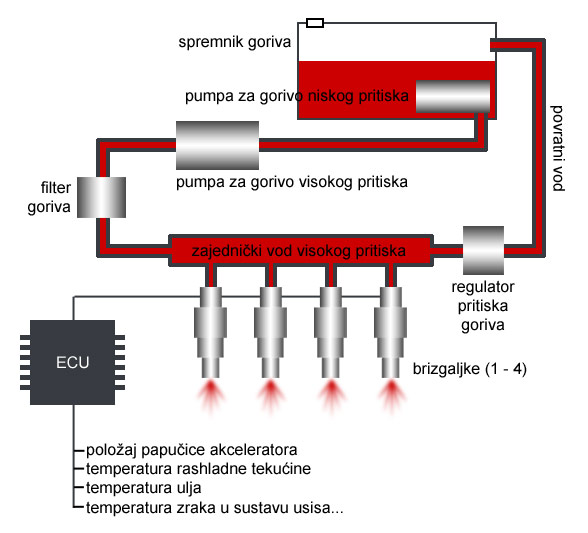
Schematic representation of an electronic fuel injection system
The story looks like this: pressing the accelerator pedal moves the butterfly in the suction pipe. A sensor that reads the position of the butterfly sends this information to the engine computer (ECU - Electronic Control Unit, for some and Centralina electrónica), which, with some other parameters received, determines the pulse width (duration). This pulse is actually the time the injector is opened and during which the fuel is injected into the suction pipe (idling can only take 2 milliseconds). Of course, the fuel is fed to the injector by tubes starting from the pump.
The usual fuel pressure delivered by the high-pressure pump in vehicles with electronic injection is 35 to 200 bar, and since the pressure is constant, it is clear that the amount of fuel injected is determined solely by the pulse width (say here and the fuel pressure it creates fuel pump low pressure is 4 to 6 bar). The excess fuel that can be generated by the injection system during slow engine running is returned to the return pipe back to the return water tank.
There are three basic versions of the injection system and they are related only to the position of the injector. We believe, namely, that the injection system today really no longer makes sense to divide into mechanical and electronic, given that the latter are represented in almost all new cars.
- Central injection is the simplest version in which the injector is placed at the beginning of the suction branch. This system, despite its simplicity (and low price) is still not ideal because the fuel is not distributed evenly in the cylinders.
- the single injection system (or multi-point injection) uses one injector for each cylinder and places it as close as possible to the intake valve. This system is more efficient because it achieves a more correct ratio of fuel and air.
- The direct fuel injection system features a injector located in the cylinder head and injects fuel directly into the cylinder, during the compression stroke. Such a system is the most efficient in terms of fuel energy utilization, and thus the most environmentally friendly.
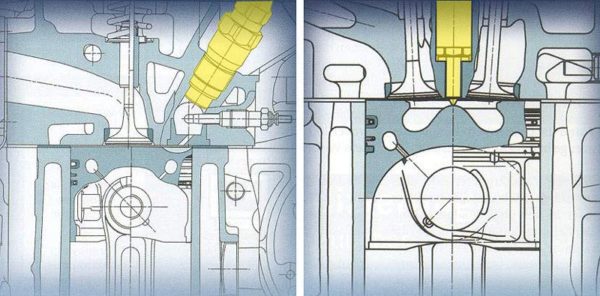
Diesel engine with vortex (left) and direct injection (injectors shown in yellow)
Diesel engines have always used fuel injection. It used to be solved with a syringe placed in a special atrium, and today it is almost the only solution that applies direct injection. Also, fuel was once delivered by diesel engines (ie their injectors) to individual lines that led from a high-pressure pump (common in our country: "Bosch pump") to each separate injector.
Today, the most common solution is the so-called Common Rail, a common high pressure fuel line that connects all injectors. But it is important to emphasize that the injection system for diesel engines use significantly higher pressure than those for gasoline engines. Thus, the fourth-generation Common Rail system of Bosch, a German plant, operates at a fuel pressure of more than 2000 bar. In part, this is due to the fact that significantly higher pressures develop during the compression stroke of diesel engines.
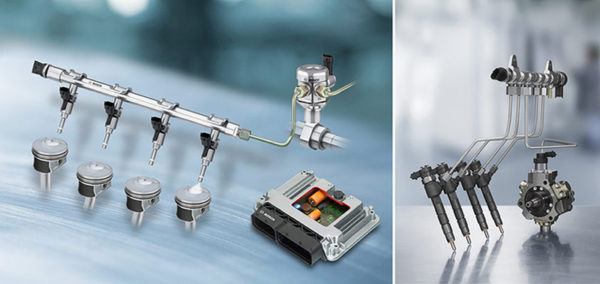
Direct Injection System for Gasoline Engine (Left) and Common Rail 2.2 (Robert Bosch GmbH)
The Common Rail system is named after the common high-pressure fuel line that supplies all injectors. But, although it sounds very logical, gasoline engines used a similar (if not the same) technology even before the term appeared. The Common Rail diesel for cars was developed by Magneti Marelli and Centro Ricerche Fiat, and the project was soon sold to the German factory Robert Bosch GmbH. The first cars powered by a diesel engine and equipped with a Common Rail system were the 156 Alfa Romeo 1.9 220 JTD and Mercedes-Benz 611 CDI (OM 1997 engine).
Finally, some more issues need to be addressed regarding the comparison of the operation of the injection system and the carburetor, which we discussed in the previous chapter. Injection e.g. it does not have to use a special petrol supply for acceleration (it is an additional tube that opens at the carburetor when the accelerator pedal is pressed abruptly), but this problem is solved by correcting the pulse width. Also, the injection has solved the problem of cold start of the engine, but unlike the "choke" in the carburetor (increased fuel supply), here it is solved by a special program, stored in the engine computer, whose work is related to data from the oxygen sensor.
Let's not forget…
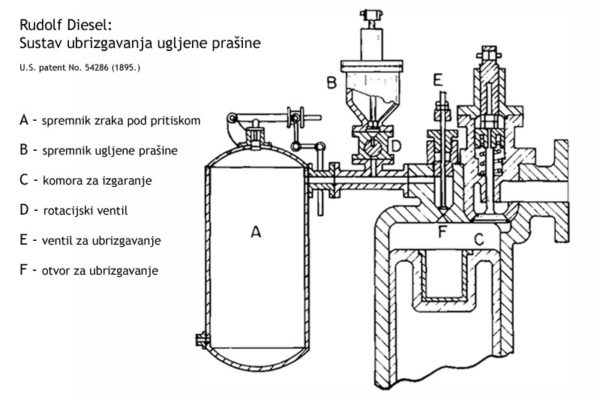
Diesel injection system for coal dust injection
As is often the case, today's marketing tries to declare many technical solutions "revolutionary", "the last word in technology" and other well-known epithets of this kind. Of course, fuel injection in the broadest range of the term is not a particularly new thing. This applies to the fuel injection method itself (as a difference from the carburetor), to the Common Rail system and to the direct injection of fuel into the cylinder (both in the case of diesel and petrol engines).
The first attempt to construct a fuel injection system was made by Rudolf Christian Karl Diesel in 1893. It was a coal dust engine that was injected into the cylinder by compressed air. The project soon failed because the first such engine exploded when trying to start.
Diesel was not discouraged and soon developed a new system of injecting oil through pressurized air, which proved to be very successful. Variations on the theme soon became commonplace in a variety of machines, the first significant next step being made by James McKechnie of the British factory Vickers Ltd. in 1910 when he developed a fuel injection system that used a mechanical pump and a camshaft-activated injector.
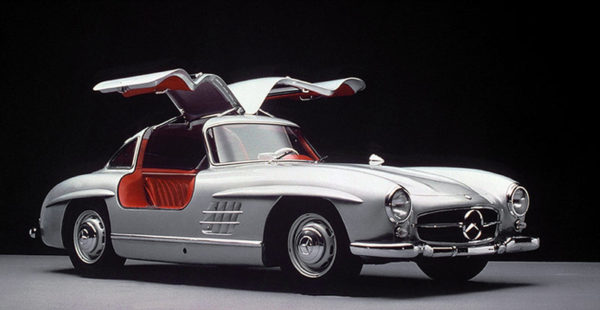
300 Mercedes-Benz 1954 SL (Daimler AG)
In 1913, the Vickers factory developed the first Common Rail injection system, in which the pump delivered fuel to a tank (common water) from which it was distributed to each cylinder separately. The pressure in the system was about 345 bar.
In 1925, Swedish engineer Jonas Hesselman introduced his direct-injection gasoline engine. It was a "hybrid" engine, a kind of mixture of diesel and gasoline engine that used gasoline to start work (lighting the mixture with a spark plug), and when it warmed up enough, it continued to run on gas oil (diesel fuel) or kerosene, according to the principle of operation diesel engine.
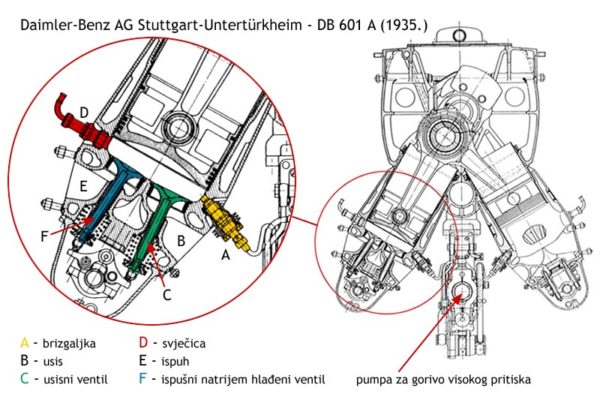
Daimler-Benz DB 601 V12
Direct fuel injection in gasoline propulsion machines entered mass application on aircraft engines during World War II. war *, and the first commercial car system was developed by Robert Bosch GmbH, 1952. After the first attempts, probably the most famous car, among the pioneers of direct injection, was certainly Mercedes-Benz 300 SL from 1954. Its 3-liter in-line 6-cylinder engine developed 158 kW (215 hp). It is interesting to mention that this is the same engine that developed 300 kW (86 hp) in the carburetor version (sedan 117).
* A typical example is the 601 Daimler-Benz DB 1935 engine: petrol "reverse V12" (crankshaft at the top), volume 33921 cm3, diameter x stroke 150 x 160 mm, compression ratio 6,9: 1, 4 valves per cylinder (sodium cooled), one camshaft in each head, direct fuel injection, 1 centrifugal compressor, maximum power 865 kW (1176 hp) at 2500 rpm, specific power 25,5 kW / l (34,7 hp / l) ) (data for DB 601 A series).
The final version of this engine, the DB 605 from 1942, had a volume of 35658 cm3 and developed 1324 kW (1801 hp) at 2800 rpm with the help of additional injection of a mixture of methanol and water (MW 50). This achieves a specific power of 37,1 kW / l (50,5 hp / l) (data for the DB 601 AM series).
Author: AUTONET.HR
Retrieved from: www.autonet.hr
Recommendation of similar texts:
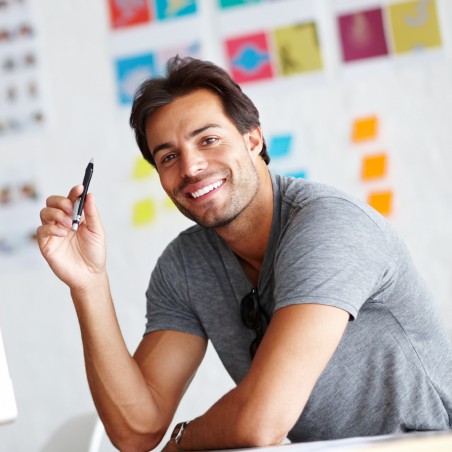
Hi there, I am Mladen and I am an auto enthusiast. I started this blog years ago to help like minded people share information about latest cars, car servicing ideas, used car info, exotic cars, and auto technology. You will find helpful articles and videos on a wide variety of cars - Audi, Mercedes, Toyota, Porsche, Volvo, BMW and much more. Ping us if you have anything cool to share on latest cars or on how to make older cars more efficient, or just want to say hi!