Brake Fluid
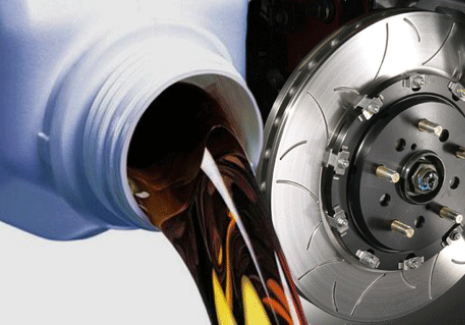
Brake Fluid
Fluids for hydraulic brake systems of motor vehicles
The braking system of motor vehicles is the most important factor for driver safety, and therefore very stringent requirements are set that the brake fluids must satisfy. These are, above all, high boiling points, good low temperature behavior, corrosion protection, adequate lubrication capability, and compatibility with sealants.
In hydraulic braking systems of motor vehicles, liquids containing mineral oils (LHM - a special fluid for central hydraulics of Citroen vehicles) or polyglycol and glycol ether based liquids can be used as a medium for transmitting brake force. Requirements for special fluid (LHM - Liquide a base minerals pour hydraulique de vehicules Citroen) for Citroen vehicles are defined in the specification CITROEN B 712710. Includes requirements for very good rheological properties, especially at low temperatures, as well as compatibility with sealants. LHM fluid is used for those systems that are marked in green. It must not be mixed with or mixed with any other fluid.
LHS 2 fluids based on synthetic and vegetable materials are used for the hydraulics of Citroen vehicles, which are marked in black, however, these vehicles are of little use.
The development of silicone fluids has not yet been completed, and due to their high cost, they are only used on race cars where special technical interventions have been carried out.
Glycol ether and polyglycol based brake fluids are most widely used with the addition of suitable anti-corrosion and oxidation additives. Their properties are defined by the following standards and specifications:
- ISO 4925.
- SAE J 1703
- FMVSS 116 for DOT 3, DOT 4, DOT 5
Specifications FMVSS 116 (Federal Motor Vehicle Safety Standard) for DOT 3, DOT 4, DOT 5 determine: change in viscosity at low temperatures, corrosion properties, resistance to changes in temperature, oxidation stability, tendency to evaporate, behavior towards elastomers (seals) and resistance to water.
Table 1: Basic requirements for brake fluids
FM VSS 116
|
ISO
4925
|
SAE
J 1703
|
||||
DOT 3
|
DOT 4
|
DOT 5.1
|
DOT 5
|
|||
Boiling point of dry liquids,0C, min.
|
> = 205
|
> = 230
|
> = 270
|
> = 260
|
> = 205
|
> = 205
|
Boiling point of wet liquids,0C, min.
|
> = 140
|
> = 155
|
> = 185
|
> = 180
|
> = 140
|
> = 140
|
Maximum viscosity at - 400C, mm2/s
|
<1500
|
<1800
|
<820
|
<1900
|
<1500
|
<1800
|
Maximum viscosity at 1000C, mm2/s
|
> 1,5
|
> 1,5
|
> 2,1
|
> 1,5
|
> 1,5
|
> 1,5
|
Classification of brake fluids by base type based on FMVSS standard 116:
- DOT 3: polyalkylene glycol
- DOT 4: blend: (poly) glycol ether and borate ester
- DOT 5.1: borate ester
- DOT 5: silicone fluid (Important: Do not mix DOT 5 with DOT 3, DOT 4 and DOT 5.1)
Glycole brake fluids effectively protect against corrosion and wear, well tolerate low temperatures. The negative property of glycol ethers is hygroscopicity, ie moisture absorption. However, this is also an advantage because hygroscopic liquids have a gradual drop in boiling temperature (steam plug appearance) with the penetration of moisture into the system, while non-hygroscopic liquids (oil-based) have an instantaneous steam plug appearance and brake pedal "decay". They constantly absorb moisture from the air and from the road through openings in the tank as well as through elastic pipelines and seals on the drive shafts. During the braking process, kinetic energy is converted into heat. Most of this heat is transferred to the surrounding air, but partly to the brake fluid. For that reason, one of the most important characteristics is the boiling point of the liquid.
SAE J 1703 - The Society of Automotive Engineers (SAE) in 1958. developed two fluid specifications for the SAE J70 R1 and SAE J70 R2 brake systems. They have been refined so that the latest SAE J 1703f is the basis for all other fluid specifications for brake systems. The requirements for boiling point and kinematic viscosity at - 40 are particularly emphasized0C.
ISO 4925. - This fluid specification for brake systems was developed in 1978 by the ISO association. It is similar to the specification of SAE J 1703 DOT 3, but additional requirements have been introduced regarding the corrosivity of liquids and the swelling of natural rubber sealing materials. The requirements for these specifications are shown in Table 1.
The moisture content of the brake fluids increases by 2 to 4% per year. This reduces the boiling point and results in the formation of vapor plugs and gas bubbles, which have a very negative effect on the efficiency of the brake system and lead to brake failure. The critical point is when driving downhill on a very warm day with frequent use of the brake. In this case, a high temperature is transmitted to the brake fluid. If it is contaminated with an unacceptable amount of water, it can cause so much steam that the piston can no longer generate high pressure causing the brake system to fail.
The boiling point of the wet liquid is the temperature at which the first gas bubbles form. With a water content of 5%, the boiling point of the DOT 3 fluid falls below the critical (140 0C), which means it must be replaced. Because DOT 4 and DOT 5 fluids are less hygroscopic and have a higher boiling point, the use period is longer than the DOT 3 fluid use period and the brake system reliability is higher. New models of vehicles with ABS use brake fluid according to DOT 5 specification. DOT 5 brake fluids are based on silicone oils. Further development of the fluid goes in the direction of borate estersmarked with DOT 5.1. Do not mix DOT 5 with other brake fluid categories: DOT 3, DOT 4, or DOT 5.1.
Motor vehicle manufacturers recommend replacing the brake fluid every two years. The shelf life of the brake fluid in the manufacturer's original packaging is unlimited, provided they are protected from the weather, especially moisture. The manufacturer's regulations must be strictly adhered to, since the materials used to make the seals (natural rubber - NR or styrene butadiene rubber - BBR) do not tolerate another type of oil. The consequence is the immediate destruction of the brake system.
Inefficient braking can also occur due to the wear of the erasers in the master or service cylinders, which can be noticed by the soft operation of the brake pedal due to the air entering the system.
Oil leakage can be very dangerous as it causes the brake system to fail, so the system must be monitored regularly. There must always be sufficient brake fluid in the tank, and if it is to be refilled more frequently, it is an indication that there is oil leakage in the brake system.
In most cases of malfunctioning and blocking of the brakes in operation, the maintenance and control of the braking system is defective. The cleanliness of the brake fluid is of paramount importance for the safety of the brake system. After replacing the brake fluid or in cases where air enters the system, aeration (ventilation) must be carried out.
The gap between the jaws and the drum or disc and discs must be sufficient, otherwise friction may occur and high temperatures may occur which cause the brake fluid to overheat and evaporate.
Potential hazards due to inadequate brake fluid:
- Brake failure
- Slow brake response
- Corrosion of metal parts
- Friction and wear of system parts
- Liquid leaks due to defective seals
- High and low temperature problems
In order to avoid these risks, the quality of the brake fluid must be taken into account, ie it must have: high boiling point, adequate low viscosity at low temperatures, excellent corrosion protection, excellent lubrication, compatibility with elastomers of seals, optimal thermal stability as and excellent low temperature stability.
Boiling point
The presence of water in the brake system can never be completely prevented. On average, the brake fluid absorbs 1% to 1,5% of water during the year. This, of course, has the effect of reducing the boiling point of the brake fluid. Braking friction causes heat to be transmitted through the cylinder to the brake fluid, with the fluid temperature rising above 1500C. At these high temperatures, the evaporation of the water present is in the form of vapor bubbles, which, unlike liquids, are compressible and cannot transfer the pressure from the brake pedal to the brake cylinder of the wheels, which can cause the brake pedal to fail and brake failure. For this reason, good quality brake fluid must have a high boiling point and the ability to prevent vapor bubbles from forming.
Viscosity at low temperatures
The transmission of braking force from the brake pedal to the brake cylinder of the wheel must be transmitted immediately - in a split second. This can only be achieved with a correspondingly low viscosity of the brake fluid. At low temperatures, the viscosity of the brake fluid increases, with the pressure being transmitted more slowly to the brakes, ie a slower braking reaction. Due to the optimal braking speed, the brake fluid must have the appropriate viscosity even at the lowest ambient temperatures.
Corrosion protection
The braking system consists of various metals: steel, cast iron, aluminum, brass and copper. The brake fluid must contain an effective additive that reliably protects the metal parts from corrosion.
Lubrication
In order to prevent friction, the brake fluid must have excellent lubricating properties. As is known, the effects of friction are: wear, abrasion and temperature rise.
Compatibility with seal elasomers
Elastomers are used to seal the brake cylinders to prevent fluid from leaking between the piston and cylinder. The brake fluid must contain the necessary agents to ensure gentle swelling of the elastomer, ensuring reliable sealing and preventing the brake fluid from leaking.
Thermal stability
In extreme operating conditions, the brake fluid temperature exceeds 1500C. Brake fluids are required to be chemically and thermally stable at these temperatures. To ensure optimum thermal stability, the brake fluids must contain quality components - glycol ethers and special inhibitors.
Low temperature stability
To prevent the risk of brake failure at low temperatures, the brake fluid requires excellent stability at extremely low temperatures, up to -500C.
Source: www.nisotec.eu
Recommendation of similar texts:
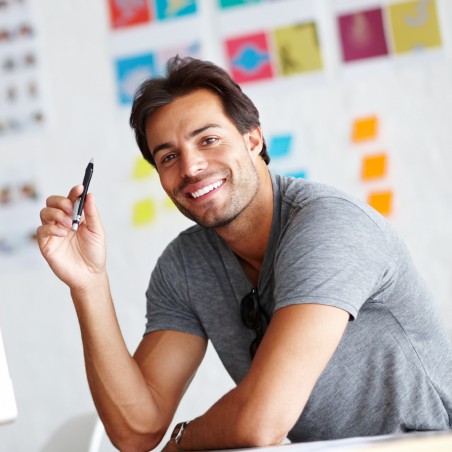
Hi there, I am Mladen and I am an auto enthusiast. I started this blog years ago to help like minded people share information about latest cars, car servicing ideas, used car info, exotic cars, and auto technology. You will find helpful articles and videos on a wide variety of cars - Audi, Mercedes, Toyota, Porsche, Volvo, BMW and much more. Ping us if you have anything cool to share on latest cars or on how to make older cars more efficient, or just want to say hi!